As far as I know! I'm the only guy who produces dovetail joints this way..So I thought I'd better record the method while I'm still able to do so....The Main instrument that I produce is a copy of the famous Martin Soprano Ukulele... whether it be style 1, 2, or 3 or whatever.. they all have one thing in common "the scribed fitted compound dovetail joint".
If the instrument has a flat ended upper bout where the neck joins (And many do!) the dovetail cutting is pretty standard stuff and there is lots of info on the web already on how this is achieved....But if (Like Martin uke's) the upper bout is radiused, then the dovetail joint becomes a lot more complicated..To make a good fit with this type of joint, the sides of the male neck joint have to be shaped / scribed in to fit the radius.... Luthiers and builders of Uke's Mandolins and Guitars etc: normaly do this job with fine saw cutting and shaping with chislels..and then sliding fine abrasive shims in between the mating surfaces of the joint ...This is very demanding work and requires a lot of skill..In the past I did my first radiused dovetail's by hand also, and I soon learned what a difficult job it was, and it could take hours of work before I was satisfied with the fit..so I put my thinking cap on and came up with this method, that I will now reveal...it's based around the use of the "Router and the Bandsaw".
The first thing to remember is that the male dovetail has 3 constants ..Angle "A", Angle "B" and Radius "C" as shown in the sketch below...These dimensions will vary depending on the size and type of instrument being made.but they can be calculated by simple Trig: or measuring with a ruler and protractor from scale drawings.

THE FEMALE PART OF THE JOINT
This is cut into the neck block prior to fitting it and gluing it into the uke body..I do this with a milling machine
I made, by converting and old pillar drill some years ago...I built a special jig and set up that accurately cuts the female slot in to the Heel block at the required angle..There is nothing new here, and this can be done by several different router methods using jigs and templates...Here is a pic' of the set up.
Before the block is fitted into the body it must be radiused to suit the radius of the uke's upper bout.
This is done with a simple set up on the disc sander...no explaination required here the picture shows all.
And here it is, fitted into the Soprano body..the female dovetail area will now be trimmed out with a razor saw and chisel ready to accept the male end when it's ready...(Don't get too excited it's only a ukulele)

NEXT on to "the main bit"....
THE MALE PART OF THE JOINT ????
make sure that the end of the neck is square and at 90 degrees
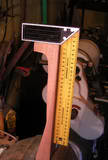
Ist thing here to remember is... Angle "A" in the sketch ..In my case this is 2 .5 degrees.
I use a standard type "Router Template Jig" for this operation.. I made this myself .
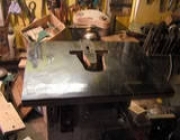
And here is a view from the underside...(note the strip of 3mm plexy glass set across the jig to produce the 2.5 degree angle "A")
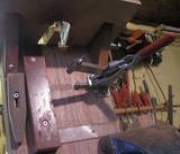
After i set the neck in the jig at Angle "A"....I start routing....When it is cut this results in a male type dovetail that is shorter at the fretboard end than the heel tip end....Here is the neck set up at a 2.5 degree angle in the jig.....*Note* I use the left hand side of the neck blank as a datum side... it is 30mm from the centreline of the neck.
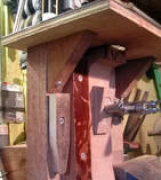
And here is the neck following routing. ...The Back end of the dovetail (If you know what i mean ??) is now slightly higher than at the front...As it should be, due to the 2.5 degree angle...I am aware that cutting a dovetail like this at 2.5 degrees will alter the profile of the angle "B" slightly.but I have allowed for that in the jig design.

After routing I double check the angle
Now we are ready for the Magic bit "Machining the radius"....For this operation i designed this bandsaw jig
It consists of two main parts ..The bottom baseboard and the top radius board...
Here it is set on the bandsaw... the bottom board is set crossways at angle "B" in the sketch.
The top board slopes at angle "A" lengthways..it also pivots on the centre line from both ends at the set neck radius ..in this case 5.5 inch rad.
The bottom board must be set exactly on the centre of the bandsaw blade
between the two pivot points..also note the end stops at the lower corners of the board.
Next i make a dummy neck test piece out of some scrap wood..i make a heel at both ends so I can have more than one go at setting up the jig... I dovetail the test piece the same as the necks
I then place it in the jig to set up the cut.....with this method I'm using the bandsaw blade as a milling tool using mostly the edges of the saw teeth ..so I find it best to use a brand new blade for this job a 1/4" X 10-14 TPI blade is ideal for a nice finish..here is the saw in action ..the metal end stopscrew is for fine adjustment if needed.
(As mentioned earlier I use the edge of the neck blank as a datum @ 30mm from the centerline of the neck)
Following the test cuts the the test blank is checked for any errors.
And then a trial fit in a Uke body
Here is a close up of the test fit showing clearly the scribed cheeks of the radius.
Now I try it out on one of the real necks.... first cut one side up to the end stop
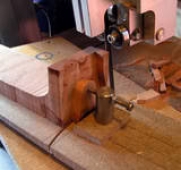
Then reverse the board.... and cut again up to the end stop
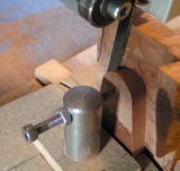
Following the cutting it looks like this...this is a nice piece of Mahogany
And here is another view...all that is required now is a small amount of handwork with a sharp chisel to clean out the corners....it just takes a few seconds.
Here is a batch of 18 neck blanks all scribed, I did all of them one side first.. then reversed the top board
And then cut the other side. Discounting the "setup time" this batch took less than 20 minutes to complete..If I had an infinate number to do, then I could have gone on all day churning them out..or until the blade wore out...They are all now ready to move on to the next stage of profiling etc:
Because all these dovetail are made to the same dimensions ..This means they are all interchangable and any neck dovetail will fit any body dovetail which makes life easy when assembly time comes along.
Here ar a few pic's of the final results of the fit.
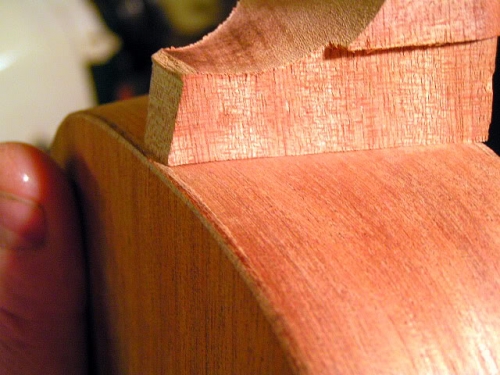
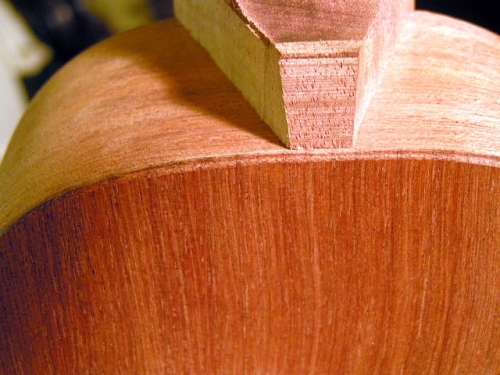
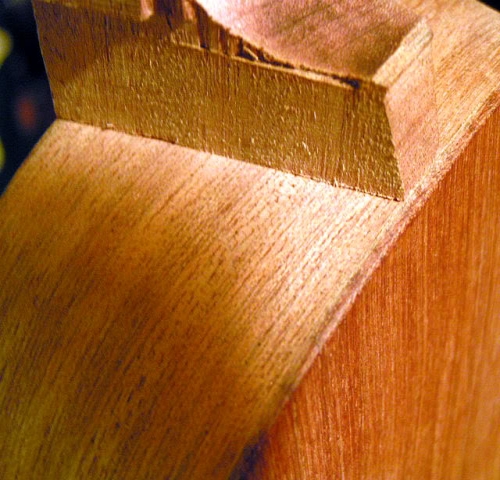
And finally on a finished ukulele
For more information of the "Complete Soprano Neck Build" from start to finish here are four slideshows that I made
Making necks part one (roughing out and dovetails)
Making necks part two (profile and turning)
Making necks part three (final shaping and handwork)
Making necks part four (fret boards fitted and french polished )
THAT'S ALL FOLK'S